Reasons and Solutions of Cracking in Deep Drawing Manufacturing
The deep drawing manufacturing process can produce various shapes of deep drawn parts. Such as cylindrical, rectangular, spherical, conical, and other irregularly shaped thin-walled parts. If it is combined with other stamping-forming processes, it can also produce parts with more complex shapes.
Considerations for Deep Drawing Manufacturing
We need to pay attention to the high width-to-thickness ratio, the length of the overhanging wall, the curvature of the large wall thickness difference, the shape of strange profiles, such as small feet, thin teeth, long legs, circular surface, inclined surface, opening, viewing point and so on. Conditions, to avoid partial or point-like scale deformation, twisting, spiral, and other defects of the profile.
Different Materials Influence on Deep Drawn Components
The deep draw component is a metal shell workpiece that uses a mold to draw a flat blank or semi-finished blank deep into an open hollow. Materials usually used for deep-draw products are low-carbon steel, stainless steel, aluminum alloy, copper alloy, etc.
- Low-carbon steel
It has the characteristic of excellent formability, high strength, and lightweight. And its cost performance is better than other deep drawing materials. The processed deep drawn shells are dimensionally stable. However, It has low corrosion resistance and requires post-treatment protection such as electroplating. Commonly used in various parts in automotive manufacturing, especially high-strength structural parts.
- Stainless Steel
Although it has the same characteristics of high strength and lightweight as low-carbon steel, stainless steel has high corrosion resistance. It is suitable for heat treatment and has good wear resistance without electroplating protection.
- Aluminum Alloy
It is characterized by being lightweight (almost 1/3 of low carbon steel), high strength, non-magnetic and non-rusting. And suitable for heat treatment and can be anodized to prevent corrosion.
- Copper Alloy
The characteristics are anti-corrosion and easy to oxidize (surface discoloration and stains). More expensive and unstable, and easy to weld. However, for moldings with inconsistent wall thicknesses, aluminum, and copper alloys are achievable.
Solution to Solve Deep Drawn Parts Cracking in the Stamping Process
The proportion of deep draw parts in the entire stamping industry is very large. Most of the products that are common in life, such as sensors, motors, electrical machinery, etc., There are too many processes full of variables, and wall cracks will occur during the deep draw processing process, which will affect product quality.
Cracking Reasons in Deep Drawing Manufacturing:
- The axial tensile stress borne by the material during deep drawingcannot be too large.
- The spacing between the punches is too small (including the global clearance and the local clearance of the punch offset).
- The lubrication is not enoughwhen deep drawing.
- Improper selection of raw materials and poor plasticity.
- It is related to the compressive strength and tensile stress of the force transmission area of the cylinder wall.
Cracking Solutions in Deep Drawing Manufacturing:
- It is necessary to reduce the width of the edge strips.
- Grind to normal value according to product requirements.
- Appropriate use of lubricating fluid in production and processing.
- Use materials with good plastic deformation or improve the workpiece quenching process.
- According to the improvement of the physical properties of the raw materials, the strength of the cylinder wall should be increased.
- According to the proper formulation of the drawing process and the design of the mold, effectively determine the degree of tensile deformation, the radius of the die fillet, and effectively improve the standard lubrication, etc., To reduce the tensile stress in the force transmission area of the cylinder wall.
Heju Stamping-30yrs Micro Deep Draw Stamping Experiences Manufacturer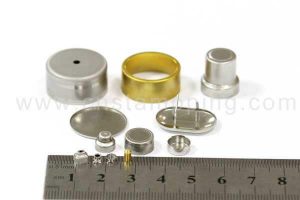
Heju Stamping is a precision stamping manufacturer with 3oyrs experiences. Specializing in the manufacturing of micro deep drawn parts and precision stamping parts in electronic industry. Our precision stamping specialists have rich experience in small deep drawing stamping project solutions. If you are looking for a deep draw stamping manufacturer, please contact us immediately for a quotation or online consultation.