Precautions for Customizing Sensor Housing
What is a Sensor Housing?
The sensor housing is the part of the sensor used to protect the internal components of the sensor from environmental factors. Sensor housings are typically made of durable materials, such as metal or plastic. And it may be waterproof, dustproof, and corrosion resistant.
The design and material selection of the sensor housing depends on the application environment of the sensor and the desired function. For example, sensors used in outdoor environments or harsh industrial environments may require a more robust housing. While sensors used in the medical or food industries may need to meet specific hygiene standards.
The sensor housing may also include connectors, cable outlets, and other accessories to facilitate electrical connections to circuit boards and components inside the sensor.
Precautions for Customizing Sensor Housing
When customizing the sensor housing, you need to pay attention to the following key issues to ensure that the housing meets the performance requirements of the sensor and has good reliability:
Material Selection
First, you need to select the appropriate material according to the application environment and performance requirements of the sensor. Commonly used materials include stainless steel, aluminum alloy, plastic, etc. Stainless steel has good corrosion resistance and mechanical strength. It is suitable for use in harsh environments. Aluminum alloy has a lighter weight and better heat dissipation performance. Plastic materials are low cost but may not be applicable in some high-temperature or high-pressure environments.
Size and Shape
The size and shape of the housing need to be precisely designed according to the internal structure and installation method of the sensor. Ensure that the housing can tightly wrap the sensor and provide the necessary protection while facilitating installation and connection with other devices.
Protection Level
Select the appropriate protection level according to the use environment and protection requirements of the sensor. The protection level is usually expressed using an IP code, such as IP67. It means that the housing can be prevented from being immersed in water for a short period (depth 1m). Ensure that the protection level of the housing meets or exceeds the requirements of the actual application scenario.
Sealing Performance
For sensors that need to be waterproof and dustproof, the sealing performance of the housing is crucial. Appropriate sealing materials and processes need to be used to ensure the sealing of the housing and prevent external liquid or dust from entering the sensor.
Heat Dissipation Performance
For sensors that need heat dissipation, the design of the housing should consider heat dissipation performance. The heat dissipation effect can be improved by adding heat sinks, opening heat dissipation holes, or using materials with good thermal conductivity.
Electromagnetic Compatibility
In some applications, sensors need to have good electromagnetic compatibility. The design of the housing should minimize the generation and propagation of electromagnetic interference to ensure accurate measurement and stable operation of the sensor.
Processing Accuracy
The processing accuracy of the housing directly affects the performance and reliability of the sensor. It is necessary to select a manufacturer with high-precision processing capabilities for production. And strictly control various parameters during the processing process to ensure the dimensional accuracy and surface quality of the housing.
Cost Considerations
When customizing the sensor housing, cost factors also need to be considered. Select appropriate materials and processes according to actual needs to balance the relationship between performance and cost.
When customizing sensor housings, it is essential to carefully consider material selection, size and shape, protection level, sealing performance, heat dissipation, electromagnetic compatibility, processing accuracy, and cost. By taking all these factors into account, it can be ensured that the customized sensor housing meets specific requirements and delivers optimal performance and reliability.
How to Meets the Performance Requirements of the Sensor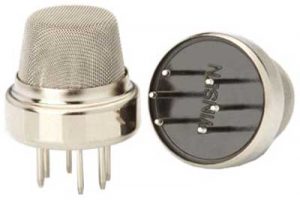
The processing technology of sensor housing parts involves multiple steps, mainly including material selection, cutting, surface treatment, welding, and final assembly. The following is an overview:
- Material Selection
Common materials for sensor housings are stainless steel (such as 304 stainless steel), aluminum alloy, copper, copper, etc. These materials have excellent corrosion resistance and mechanical properties.
- Cutting
According to the design drawings, cut and cut stainless steel straight pipe sections or steel plates. The cutting section must ensure the accuracy of the angle with the pipe wall. And the port burrs and flash must be polished.
- Surface Treatment
In order to improve the beauty and durability of the housing, surface polishing, painting, and electroplating are often performed. Surface polishing can remove burrs and flaws on the metal surface, painting can prevent rust and improve the appearance of texture. And electroplating can further enhance the anti-corrosion performance.
- Welding
The welding of the sensor housing is a key step. Common welding methods include argon arc welding, CO2 gas-shielded welding, etc. During the welding process, it is necessary to ensure the firmness and sealing of the weld while avoiding defects such as welding deformation and pores.
- Assembly
After completing the processing and surface treatment of all parts, assembly work is carried out. This includes welding and fixing the annular steel plate to the stainless steel straight pipe section. Installing the flange, connecting the sensor to the header pipe section, etc.
- Other Processes
Depending on specific needs, it may also include process steps such as coil winding, rubber lining, and explosion-proof treatment.
Summary
It should be noted that the processing technology of the sensor housing may vary depending on the specific product, material and design requirements. In actual production, operations should be strictly carried out in accordance with the process regulations to ensure product quality and performance.
In addition, for sensor housing parts involving precision machining and high-precision requirements, more advanced processing technologies and equipment may be required. Such as CNC machining, laser cutting, ultrasonic welding, etc. These technologies can improve processing accuracy and efficiency and meet higher production requirements.