How Does Automotive Low-voltage Wire Connector Terminals Plating Affect Wire Harness Design?
As automotive electronics advance, the automotive wiring harness is the car’s nervous system and plays a crucial role in transmitting power and signals. Given that the automotive wire terminals acts as the central hub that connects the wiring harness to other components, its design and plating quality significantly impact the stability and reliability of the wiring harness. This article will delve into a comprehensive analysis of the automotive wire connector terminals types and plating’s influence on automotive wiring harness design.
Automotive Wire Terminals Types
Tinned Terminals
Tin-plated automotive wire connector terminals are popular due to their low cost and good environmental stability during use. The main surface treatment options include dark, bright, and hot-dip tin. However, it’s important to note that these terminals have some limitations. For instance, their wear resistance may be weaker than other coatings, and they may have limited plug-in cycles. Additionally, over time and under higher temperatures, their contact performance may decrease, making them suitable for use in environmental conditions below 125°C. When designing tinned terminals, it’s crucial to consider high contact force and small displacement to ensure optimal contact stability.
Silver Plated Automotive Crimp Terminals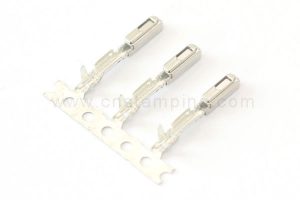
Although silver-plated terminals exhibit excellent point contact performance and can operate continuously in temperatures of up to 150°C, they are more costly and susceptible to rust in the presence of sulfur and chlorine in the air. Additionally, they are more durable than tin-plated terminals, but their resistivity is slightly higher or equivalent to tin.
Gold Plated Automotive Connector Terminals
Gold-plated terminals boast impressive contact performance and environmental stability on par with both tin-plated and silver-plated terminals. Additionally, they exhibit exceptional friction resistance. It’s worth noting that gold plating is the most costly of the three processing methods. That being said, not every terminal necessitates gold-plating. If tin-plated terminals wear down due to low contact force, they can be swapped for gold-plated ones.
The Impact of Terminal Plating on Automotive Wiring Harness Design
- Protect electrical connection components
The metal part of the terminal is plated, which can effectively prevent oxidation and corrosion of the terminal in a humid, high temperature or alkaline environment and extend the service life of the terminal.
- Optimize electrical conductivity:
Terminals plated with gold, silver, tin, and other metals have better electrical conductivity when conducting current, reducing resistance and improving transmission efficiency.
- Improve connection stability
The good conductivity and oxidation resistance of the terminal coating can maintain connection stability, prevent the wire harness from falling off or disconnecting, and ensure the normal operation of the automotive electronic system.
- Reduce maintenance costs
Using corrosion-resistant terminal coatings can reduce the frequency of wire harness maintenance, extend the life of the wire harness, and reduce maintenance costs.
- Improve the quality of the entire automotive
The high-quality treatment of the terminal plating can not only improve the reliability of the wiring harness connection but also improve the entire automotive’s quality and user satisfaction.
Selection Principles of Automotive Connector Terminal Pins Plating
- Select appropriate coating materials according to the specific use environment. For example, corrosion-resistant materials should be selected in humid environments.
- Select the appropriate plating material according to the terminal’s voltage and current requirements to ensure the terminal’s conductive performance.
- To improve connection stability and reliability, coating materials with wear resistance, corrosion resistance, and good conductivity should be selected.
- When designing terminal plating, economics, and production technology should also be considered to ensure that the cost of the terminal is controllable and the processing technology is feasible.
Summary
Selecting automotive electrical wire terminals types and plating materials is crucial when designing automotive wiring harnesses. Making sensible choices can enhance the stability and dependability of the harness. It is vital for the proper functioning of the electronic system in a vehicle. When choosing a manufacturer for wire harness production, it is imperative to prioritize material selection, processing, and connection quality control. Only reasonable and appropriate processing and connection techniques can elevate the reliability of terminal connections. Additionally, it is essential to conduct thorough quality inspections and verifications of these connections to detect and address any issues promptly, thus ensuring the stability and dependability of the wiring harness.
About Hejustamping-Professional Automotive Wire Terminals Manufacturer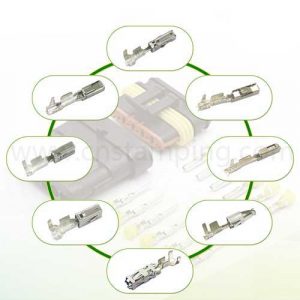
Heju Precision Electronic Technology Co., Ltd. is a reputable manufacturer specializing in designing and producing automotive wire crimp terminals. The company earned the IATF16949 system certification in 2016, which attests to its commitment to high-quality standards. With extensive experience developing low-voltage female/male connector terminals and a comprehensive quality inspection system, Heju’s terminals boast stable thermal and electrical conductivity. They meet the quality benchmarks of imported brands and can be customized to meet customers’ unique needs while achieving localized substitution.