Analysis of Prismatic Battery Stamped Components: How to Continuously Reduce Costs
With the development of the economy and technology, new energy vehicles have become a highly anticipated industry in the automotive industry. They not only meet people’s pursuit of energy conservation and environmental protection but also reduce the cost of using gasoline vehicles. However, based on the actual situation in the market, cost reduction of new energy vehicles is still a hot issue in this industry. This article will discuss the battery stamped components of new energy vehicles in detail and discuss how to reduce the cost continuously.
Overview of Prismatic Lithium Battery Stamped Components
Prismatic lithium battery stamped components encompass the sealing plate, anode collectors, cathode collectors, burst/rupture disks and terminals. These parts serve several crucial functions, including energy transmission, aesthetic enhancement, electrolyte containment, and safety protection. Additionally, they can be designed with specific attributes like corrosion resistance, shock resistance, and connectivity to suit different applications. The role of battery metal parts is pivotal in influencing the energy density, sealing, and other characteristics of lithium batteries.
Industrial Chain Structure and Price Share of Prismatic Cells Stamped Parts
When assessing cost structures and manufacturing processes, it is essential to consider that structural components. Including cylindrical and prismatic parts and aluminum-plastic films, are part of the metal material processing industry. Raw materials constitute more than 50% of production expenses, followed by manufacturing costs such as depreciation, electricity, and labor. Prismatic aluminum shell metal parts are mainly composed of aluminum alloy, copper, steel, plastic, and other materials. In contrast, the raw materials for aluminum-plastic films include aluminum foil, nylon, polypropylene, and essential adhesives.
Prismatic Batteries Dominate Domestic Market, Highly Packaging Process Costs
From the perspective of packaging technology, prismatic cells continue to dominate the domestic market. In 2023, prismatic cells accounted for 85% of the market share. The prismatic cells used in electric vehicles are also different, with higher space utilization and more flexibility. Because they need to cope with the utilization of different spaces. They will be customized for different customer requirements, which indirectly leads to slightly higher costs than cylindrical cells. There will be more types of cells and supporting production lines in the future. And production and maintenance will require expenditures, which will also be allocated to the battery cost and then reflected in the price.
Combination and Process of Battery Sealing Plate
The structure of the prismatic lithium battery sealing plate is complex and precise. And it is responsible for energy transmission and explosion-proof pressure relief. The lithium battery sealing plate is composed of more than ten components. It mainly composed of top cover, anode collectors, cathode collectors, burst/rupture disks and terminals, flip plate, battery safety vents and other structures. And its value is about two times that of the shell.
Battery Rupture/Burst Disks, High Technical Barriers
The production of rupture/burst disks for prismatic batteries is a significant technical challenge in the manufacturing process, typically achieved through stamping. Given the lack of unified specifications for prismatic cells, manufacturers have distinct specifications and explosion-proof requirements. As the standards for rupture/burst disks continue to advance, considerable investment is needed to create the necessary molds.
It is recommended to choose the standard battery rupture/burst disks that are unified by the manufacturer. It can reduce the cost of mold opening and shorten the research and development cycle to achieve the purpose of cost reduction. In the context of calling for domestic substitution, if the consistency and long-term safety of the prismatic lithium battery rupture/burst disks can be guaranteed, domestic materials can also be tried.
Hejustamping-Prismatic Battery Stamped Components Manufacturer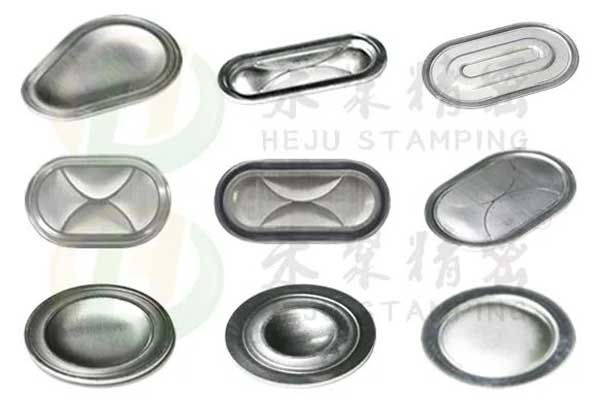
Dongguan Heju Precision Electronic Technology Co., Ltd. is a leading stamping manufacturer in China. Specializing in the production of prismatic lithium battery safety vents for new energy vehicles. As one of the earliest companies in China to develop and produce these battery vents, we have a wide range of models and specifications, with a single unit pressure range of up to 0.03MPA. Our CPK>2.0. We work closely with customers in product development and have passed the three major certification systems: ISO9001, ISO14001, and IATF16949.