Analysis of Micro Deep Draw Stamping Technology and Process
Introduction
The process of micro deep draw stampings by progressive dies is commonly used to manufacture high-precision, thin-walled parts. It loads sheet metal into a mold and applies force to form the desired shape. This process has the advantages of high efficiency, high precision, and high quality. And it is widely used in the automotive, aerospace, medical, and other industries. This article will detail the precision deep-drawn parts stamped by deep draw progressive dies from the aspects of process principle and process parameters.
The Principle of Micro Deep Draw Stamping Parts
The micro deep drawn parts stamped by deep draw dies to apply tension on the surface of the workpiece so that the workpiece is deformed. Deep draw forming of materials can be achieved by controlling the magnitude and direction of the pulling force during the forming process. During the deep drawing process, the material undergoes axial and circumferential plastic changes, thereby changing the shape and size of the workpiece.
The key technology of precision deep drawn components is to choose the shape of the mold and the position where the tension is applied reasonably. Deep draw forming of different shapes can be achieved by changing the shape of the mold and the position where the tension is applied. At the same time, we should also control the magnitude and speed of the pulling force to avoid local overstretching or breaking.
Precision deep draw stamping parts uses metal sheets as the raw material. And the metal sheet is deformed into the required shape through the coordinated action of the deep draw progressive dies.
The Process of Deep Draw Stamping
The process generally includes feeding, deep drawing, and demolding.
- Feeding: Feed the metal sheet into the mold; it is usually adopted by mechanical feeding or pneumatic feeding. During the feeding process, it is necessary to ensure that the metal sheet enters the mold accurately and that the feeding speed matches the processing speed to avoid defects such as ballasting or excessive deep drawing.
- Deep drawing: The sheet metal is stressed to deform the deep draw station. During the deep drawprocess, parameters such as stress magnitude, speed, and time need to be controlled to avoid problems such as fracture of the metal sheet or uneven stress. Typically hydraulic or mechanical actuation is used to apply the deep draw force.
- Demolding: After completing thedeep draw, slide the finished product out of the mold. Pneumatic or mechanical molding is usually used.
Parameters of Precision Deep Draw
Micro&precision deep drawn parts stamped by progressive dies require setting up reasonable process parameters to ensure the quality and dimensional accuracy of finished products. The following are several commonly used process parameters:
- Deep Draw Force:
It refers to the stress applied to the metal sheet. The magnitude of the deep draw force is related to the sheet metal’s material properties, size, and deep draw speed. Too much deep draw force will cause the metal sheet to break, while too little force will cause uneven stress.
- Deep Draw Speed:
It refers to the speed of the metal sheet during the deep drawprocess. The choice of deep draw speed should be determined according to the performance and shape of the metal sheet. If the deep draw speed is too fast, problems such as stress concentration and excessive heating will easily occur. And if the deep draw speed is too slow, the production efficiency will be reduced.
- Deep Draw Time
It refers to the duration of the metal sheet during the deep drawprocess. The length of deep draw time affects the strain and stress distribution of the sheet metal. Too long a time will lead to excessive stretching and loss of elasticity of the metal sheet. On the contrast, too short a time will affect the dimensional accuracy of the finished product.
- Mold clearance
Mold clearance is the distance between the upper and lower molds. The size of the mold gap should be determined according to the thickness and material properties of the metal sheet. Too much mold clearance will result in an oversized finished product, while too small mold clearance will result in poor surface quality.
Heju Stamping-30yrs Micro Deep Draw Stamping Experiences Manufacturer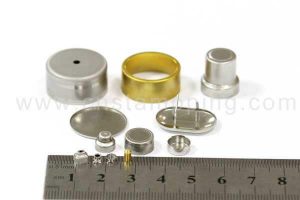
Dongguan Heju Precision Electronic Technology Co., Ltd. is an enterprise specializing in producing precision stamping parts. It has advanced equipment and technology, focuses on R&D and innovation, and has established an independent development center. Besides, In terms of deep draw forming calculation and analysis, advanced computer simulation technology is introduced to ensure the product’s process feasibility and product quality through the simulation analysis of the product’s deep draw properties and forming process. At the same time, the company has also established a perfect quality management system. We are strictly follow the production and management by the requirements of the ISO9001 quality management system.